Cannabis Product Recalls:
How Businesses Can Be Proactive in Preventing Them
A product recall is a process where a company removes a product from the market or takes corrective action due to safety concerns, regulatory non-compliance, or other issues that could harm consumers. Recalls can be initiated by the company itself, regulatory bodies, or in response to consumer complaints. The consequences of a recall can be severe, leading to financial loss, damage to reputation, legal action, and most importantly, harm to consumers.
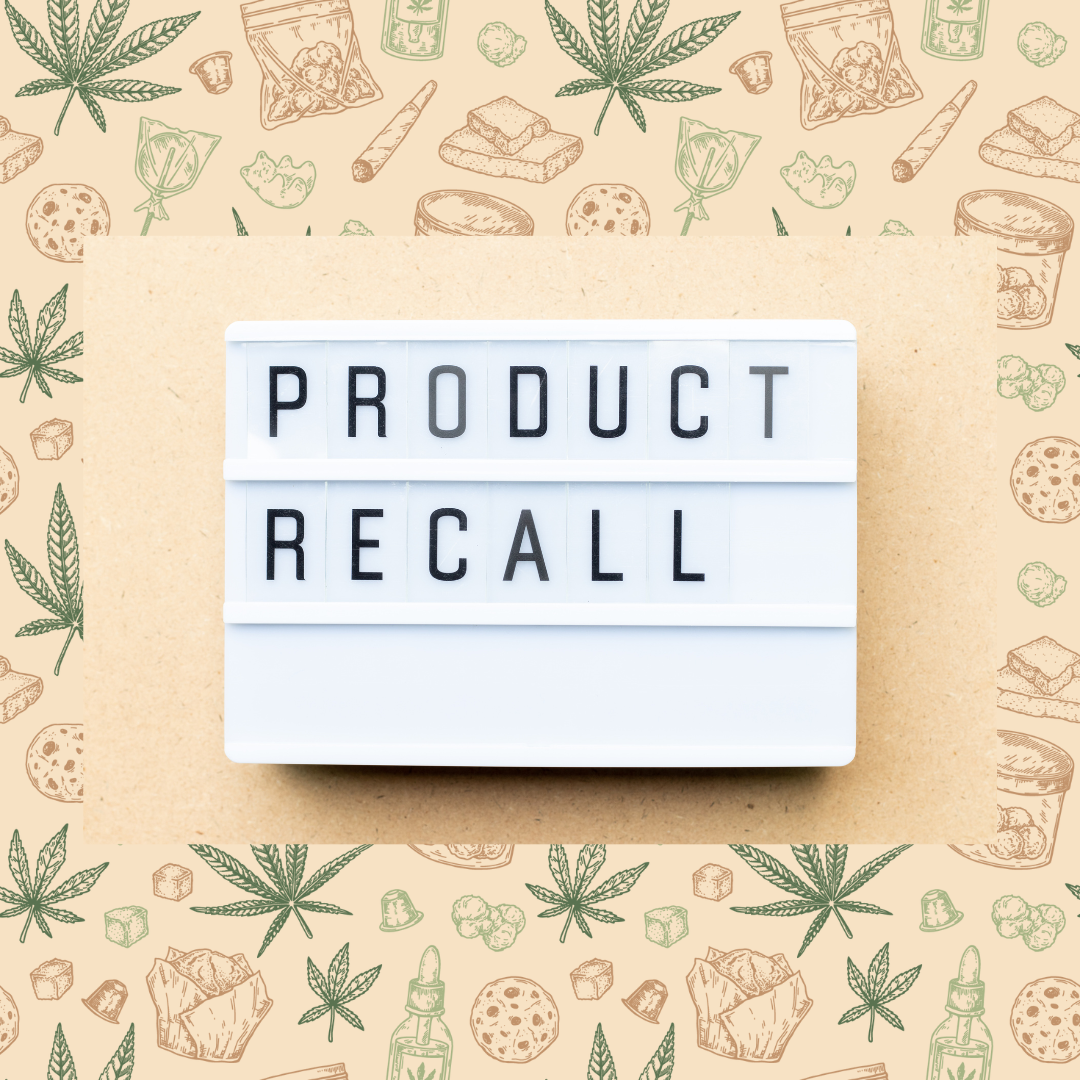
Product recalls can be triggered by a wide range of factors, including:
- Microbial Contamination: The presence of harmful microorganisms such as bacteria, mold, yeast, or other pathogens can contaminate products and cause illness.
- Heavy Metals & Pesticides: Unsafe levels of heavy metals like lead, arsenic, or mercury, as well as residues from banned or excessive pesticides, can pose serious health risks.
- Mislabeled Products: Inaccurate or incomplete information on product labels, such as incorrect potency, missing allergen warnings, or inaccurate ingredient lists, can mislead consumers and cause harm.
- Compromised Storage & Handling: Products that are initially safe can become contaminated or unsafe due to improper storage, packaging, or transportation conditions, such as exposure to extreme temperatures, humidity, or cross-contamination.
- Design Flaws: Defects in product design or manufacturing can lead to malfunctions, injuries, or other safety hazards.
- Foreign Material Contamination: The presence of foreign objects in products, such as glass shards, metal fragments, or plastic pieces, can cause injuries if ingested or used.
How Cannabis Businesses Can Be Proactive
To prevent product recalls, businesses must take a proactive approach by implementing effective recall plans, ensuring robust quality control, and fostering a culture of safety and compliance.
Develop a Comprehensive Recall Plan
A well-structured recall plan enables businesses to respond quickly and effectively in the event of a recall, minimizing the impact on consumers and the business. Key components of a recall plan include:
- Designating a Recall Coordinator: A designated individual or team should be responsible for overseeing the recall process, coordinating communication with stakeholders, and ensuring compliance with regulatory requirements.
- Clear Recall Procedures: Detailed procedures should be established for identifying, isolating, and removing affected products from the market, as well as for safely disposing of or remediating them.
- Consumer & Regulator Communication: Protocols for notifying regulatory bodies, retailers, distributors, and consumers about the recall should be in place, including clear and concise communication messages and contact information.
- Documentation & Reporting: Thorough records of recalled products, consumer complaints, investigation findings, and corrective actions taken should be maintained for traceability and future reference.
Implement Rigorous Quality Control Measures
Quality control measures are essential for identifying and addressing potential issues before products reach the market. Best practices include:
- Routine Testing: Regular laboratory testing for contaminants, such as microbial pathogens, heavy metals, pesticides, and other potential hazards, should be conducted at various stages of production.
- Packaging & Material Safety Checks: Product packaging and materials should be evaluated for safety and compliance with regulatory standards, ensuring they do not introduce contaminants or pose other risks.
- Random Sampling & Inspections: Internal audits and random sampling of products should be performed to verify compliance with quality standards and identify any potential issues.
- Supplier Verification: Suppliers of raw materials, components, and finished products should be evaluated and audited to ensure they meet quality and safety requirements.
Maintain Proper Storage & Handling Protocols
Proper storage and handling throughout the supply chain are critical for maintaining product safety and preventing contamination. Businesses should:
- Monitor Temperature & Humidity: Storage areas should be equipped with monitoring systems to ensure that temperature and humidity levels are maintained within safe and optimal ranges for the specific products.
- Ensure Clean Handling Practices: Employees should be trained on proper sanitation protocols, including hand hygiene, use of gloves and protective equipment, and cleaning and disinfection of equipment and surfaces.
- Inspect Transportation Conditions: Transportation vehicles and containers should be inspected to ensure they are clean, well-maintained, and capable of maintaining appropriate environmental conditions during transit.
Train Staff on Compliance & Safety Standards
Employees play a vital role in product safety. Comprehensive training programs should cover:
- Regulatory Compliance: Employees should be knowledgeable about relevant regulations and standards pertaining to their specific industry and job functions.
- Handling & Sanitation: Proper techniques for handling products, cleaning and sanitizing equipment, and preventing cross-contamination should be emphasized.
- Recall Response Drills: Simulated recall exercises can help employees understand their roles and responsibilities during a recall and ensure a swift and effective response.
Utilize Technology & Data Analytics
Technology and data analytics can be leveraged to enhance product safety and traceability. Businesses can implement:
- Track-and-Trace Systems: These systems enable real-time tracking of products throughout the supply chain, facilitating quick identification and isolation of affected products in the event of a recall.
- Predictive Analytics: Data analytics can be used to identify patterns and trends that may indicate potential quality or safety issues, allowing for proactive intervention.
- Sensor Technology: Sensors can be used to monitor environmental conditions during storage and transportation, ensuring products are not exposed to harmful conditions.
Additional Preventative Measures in the Cannabis Industry
Although some of the items listed below are mandatory in some legal States, not all are required and are a good reminder of the importance of going above and beyond what is mandated in the rules and regulations. It's engaging in good business practices in the cannabis industry, cultivating and selling clean products - keeping consumers safe.
- Pre-Harvest Testing: Soil, water, and plant tissue should be tested for contaminants before harvest to identify and address potential issues early.
- Supply Chain Transparency: Strict supplier qualification and verification programs should be implemented to ensure raw materials and ingredients meet quality and safety standards.
- Batch Tracking Systems: Robust track-and-trace systems should be used to track products from seed to sale, enabling traceability and quick action in case of a recall.
- Good Manufacturing Practices (GMP): Adherence to GMP guidelines ensures consistent quality and safety in cannabis production.
- Laboratory Testing: Finished products should be tested by accredited laboratories for contaminants, potency, and other quality attributes.
Preventing product recalls requires a proactive and multifaceted approach that prioritizes quality, safety, and compliance. Businesses that invest in preventative measures, such as robust quality control, comprehensive recall plans, and employee training, can significantly reduce the risk of recalls, protect consumers, and safeguard their brand reputation. By adopting best practices, staying informed about regulatory changes, and learning from past recalls, businesses can ensure product safety and maintain long-term success in an increasingly competitive and regulated market.
ICS Consulting specializes in Compliance based services, such as Third-Party State Regulatory Audits, State and Local License Application Support, Technical Writing, Standard Operating Procedures Development, Worker Safety, QMS, OSHA Compliance, Metrc Seed-to-Sale Support, Compliance Operations Training, Employee Retention Solutions, and Employee Onboarding. For more information on how ICS Consulting Service can help your Cannabis Business, book a 30-minute discovery call and we'll help you map out your next steps to be successful in the Regulated Cannabis Industry.