Worker Safety in your Cannabis Operation
Written by Jenny Germano
Cannabis operations and Occupational Health and Safety go hand in hand. Whether you’re an existing licensed operator or applying for a license. All Cannabis facilities have some type of work hazard, and employees can get hurt on the job in a variety of situations. Complying with OSHA standards, can prevent and/or minimize the risks for employees while on the job and performing their duties. It is the responsibility of the business owner and/or company to ensure employees are safe in their work environments, and employees know their rights related to occupational health and safety.
There is a “myth” going around, since Cannabis is federally illegal, that Cannabis businesses are not mandated to comply with (OSHA) federal standards. That is not true. There are a lot of cases out there where OSHA has given out violations to operators, and recently one Cannabis company had press around an employee death due to the lack of ventilation in regards to kief “dust” while they performed their job duties.
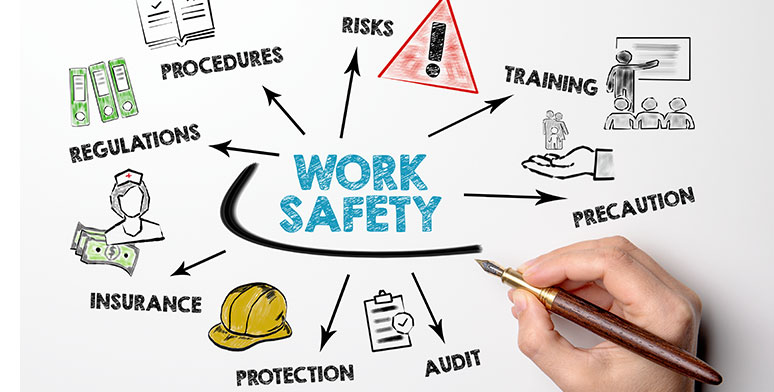
Cannabis operations are on the radar when it comes to OSHA, especially with legalization spreading across the United States. We’ll start seeing more violations handed out, as more operations get licensed.
Per OSHA General Duty Clause: Each employer shall furnish to each of his employees employment and a place of employment which are free from recognized hazards that are causing or are likely to cause death or serious physical harm to his employees;
- Shall comply with occupational safety and health standards promulgated under this Act.
- Each employee shall comply with occupational safety and health standards and all rules, regulations, and orders issued pursuant to this Act which are applicable.
Every cannabis license type: Dispensary, Cultivation, Manufacturing Facility, Testing Lab, and Transporters need to be engaged with OSHA standards at their physical operations at some level.
We recommend that compliance officers, safety manager, or management, and employees engaged with daily work hazards, take a 10-Hour and/or 30-Hour OSHA General Industry course, either on-line or in person. It’s important to understand and recognize existing hazards in a Cannabis facility, in fact in some States for example like California (Cal/OSHA) require this training as a mandatory requirement for Cannabis operators.
Companies should have these plans in place at their licensed facility. Some plans will differ depending on the license type. For example, a dispensary will have less hazards as it relates to chemicals but it still has chemicals on site for cleaning and sanitizing. A manufacturing and cultivation facility will need to communicate a PPE plan and what protective equipment employees need to be wearing versus a transporter might not have any PPE gear other than gloves or a uniform.
There are all types of hazards, such as slipping, tripping, falling, ladders, chemicals being used or applied to plants, ergonomics such as repetitive motion like trimming and packaging, operating equipment like extraction units or plant buckers or trim barrels, machine guarding, hearing loss, respiratory, and emergency events like fire or chemical spills are to name a few.
Here are a few plans Cannabis Operators need to have as part of their Operational SOPs.
Hazard Communication Plan (HAZCOM)
The Hazard Communication Standard requires employers to inform employees of the hazards and chemicals they are exposed to, and the protective measures available. All workplaces must have a written plan describing how the Hazard Communication Standard will be implemented in that facility. The steps for implementing an effective hazard communication plan are:
- Obtain a copy of the standard from OSHA and designate an individual responsible for implementing this standard.
- Prepare and implement a written plan which includes how the facility will meet the standard for each chemical in the workplace
- Ensure ALL containers are labeled correctly.
- Maintain Safety Data Sheets (SDS).
- Inform and train employees in the hazardous chemicals before their initial assignment, and whenever new hazards are introduced. Employees must understand SDSs and labeling.
- Evaluate and assess your program.
Emergency Action Plan (EAP)
An Emergency Action Plan spells out what should happen at a specific workplace during an emergency, per OSHA (1910.38). The minimum elements of a written emergency plan include:
- Procedures for reporting a fire or other emergencies
- Procedures and exit routes for emergency evacuation
- Procedures to be followed by employees who remains to operate critical plant operations before they evacuate
- Procedures to account for all employees to obtain more information about the plan.
- Explanation on how the company will notify employees in case of an emergency.
Fire Prevention Plan (FPP)
A fire prevention plan must be written, kept in the workplace, and made available to employees for review. An employer with ten or fewer employees may communicate the plan orally. Local municipalities may have different guidelines for marijuana facilities. At minimum, the fire prevention plan must include:
- A list of all major fire hazards
- Proper handling and storage procedures for hazardous/flammable materials
- Potential ignition sources
- Protection equipment necessary to control each major hazard
- Procedures to control the amount of flammable and combustible material stored in the facility
- Procedures for regular maintenance of safeguards on potential ignition sources
- Name of employee maintains fire prevention equipment
- Name of employee operates fire control equipment
- Anything necessary for an employee’s self-protection
- Procedures for clean-up and removal of combustible material
PPE Assessment
The PPE standard prescribes a hazard assessment for the entire workplace and each individual job or task. If a process or work practice changes the employer should re-evaluate PPE needs to determine if the existing PPE program remains suitable and protective for employees. The steps in a PPE Assessment are:
- Assessing the workplace for hazards
- Implementing engineering and administrative controls to control or eliminate or minimize these hazards Selecting appropriate PPE for hazards that cannot be eliminated or controlled through engineering and work practices
- Informing employees why the PPE is necessary and when it must be worn
- Informing employees of proper use, the limitations, and how to care for, maintain, clean, and dispose of the PPE.
- Demonstrating understanding of the program by employees.
Lastly, these are not all the requirements for Cannabis operators as it relates to OSHA. We just picked a few to provide some context. For more information or a consult regarding implementing these standards in your operations, reach out to info@icsconsultingservice.com.
ICS Consulting specializes in Compliance based services, such as Third-Party State Regulatory Audits, State and Local License Application Support, Technical Writing, Standard Operating Procedures Development, Worker Safety, QMS, OSHA Compliance, Metrc Seed-to-Sale Support, Compliance Operations Training, Employee Retention Solutions, and Employee Onboarding. For more information on how ICS Consulting Service can help your Cannabis Business, book a free 30-minute consult and we'll help you map out your next steps to be successful in the Regulated Cannabis Industry